Introduction to Dairy Processing Plants
Dairy processing plants are the backbone of the dairy industry, transforming raw milk into a diverse range of products that grace our tables daily. From the creamy yogurt that complements your breakfast to the cheese that tantalizes your taste buds, these facilities are pivotal in ensuring that dairy products are not only available but also safe and of high quality.
Imagine a world without the convenience of grabbing a carton of milk or a tub of butter from your local store. Sounds complex, right? That’s where dairy processing plants, also known as milk processing facilities, come into play. These plants are equipped with advanced technologies and machinery, such as pasteurizers and homogenizers, which are essential for processing milk efficiently and safely. By adhering to stringent hygiene and safety standards, these facilities ensure that the milk is free from harmful bacteria, thus safeguarding public health.
The role of dairy processing plants extends beyond just processing. They are instrumental in maintaining the freshness and extending the shelf life of dairy products through processes like pasteurization and ultra-high-temperature processing (UHT). This not only helps in reducing food waste but also allows dairy products to reach a broader market, including areas with limited access to refrigeration.
Moreover, these plants support the economy by providing jobs and contributing to the dairy supply chain. They enable dairy farmers to focus on milk production while ensuring that the milk is transformed into a variety of products, from traditional offerings like butter and cream to innovative options like lactose-free milk.
In essence, dairy processing plants are vital in bridging the gap between milk production and consumer demand, ensuring that dairy products are accessible, safe, and of the highest quality. As the dairy industry continues to evolve, these plants remain a cornerstone of its success, continually adapting to meet the needs of consumers and the market.
What Are Milk Processing Plants?
Milk processing plants are specialized facilities where raw milk is transformed into a variety of consumable dairy products. These establishments are critical in the dairy industry, as they handle and process milk to ensure it meets safety and quality standards before reaching consumers. But what exactly happens within these plants, and why are they so significant?
At their core, milk processing plants are places where milk undergoes several essential processes. These include pasteurization, which eliminates harmful bacteria, and homogenization, which ensures a uniform texture. The milk is also standardized to achieve the desired fat content and packaged for distribution. This transformation process is crucial for producing a wide array of dairy products such as cheese, yogurt, butter, and cream.
Beyond processing, these plants play a pivotal role in the dairy industry by ensuring that the products are safe for consumption and have a longer shelf life. This not only supports public health but also reduces food waste. Through rigorous quality control measures, milk processing plants help maintain the nutritional integrity of dairy products, making them a reliable source of essential nutrients like calcium, protein, and vitamins.
The economic impact of milk processing plants is substantial. According to the International Dairy Foods Association, the U.S. dairy industry supports over 3.3 million jobs and contributes significantly to the economy, with an overall impact of $753 billion (source). These plants provide employment opportunities and stimulate local economies by sourcing raw materials from nearby dairy farms.
In summary, milk processing plants are indispensable to the dairy industry. They ensure that the milk we consume is safe, nutritious, and available in various forms to meet consumer demands. As the industry continues to grow, these plants will remain vital in supporting public health and economic stability.
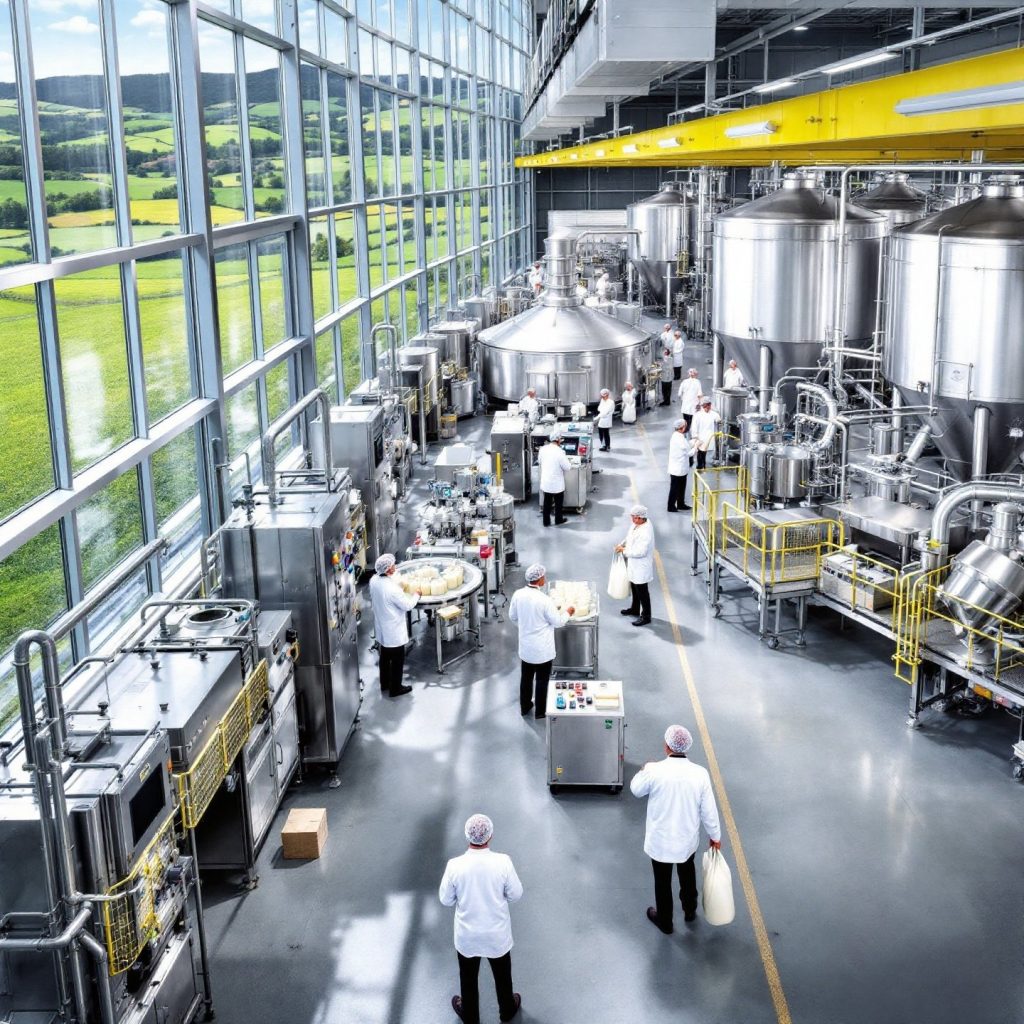
Key operations in transforming raw milk into dairy products (AI-generated)
Key Operations in Dairy Processing
Understanding the intricacies of milk processing operations is essential for appreciating how raw milk is transformed into the dairy products we enjoy daily. Each step in the process is meticulously designed to ensure safety, quality, and efficiency. Let’s delve into the key operations involved in dairy processing, which are crucial for maintaining the integrity of dairy products.
- Reception and Testing of Raw Milk: Upon arrival at the processing plant, raw milk is immediately tested for quality and safety. This step involves checking for temperature, smell, and conducting various laboratory tests to ensure the milk meets regulatory standards. It is the first line of defense against contamination, ensuring only high-quality milk enters the production line.
- Separation: Using centrifugal forces, this operation separates skim milk from cream. This is a fundamental step that allows dairy plants to produce a range of products, from low-fat milk to rich creams. Clarifiers are also used to remove unwanted particles, ensuring purity.
- Standardization: This process adjusts the fat content of milk to specific values, ensuring consistency across products. Standardization is crucial for delivering uniform products to consumers and is achieved by blending cream and skim milk in precise ratios.
- Pasteurization: A vital step in ensuring food safety, pasteurization involves heating milk to destroy harmful pathogens. The most common method, High Temperature Short Time (HTST), efficiently processes milk while preserving its nutritional value.
- Homogenization: This process breaks down fat globules in milk, preventing the formation of a cream layer and ensuring a smooth texture. Homogenization is essential for maintaining the desired consistency in products like milk and yogurt.
- Packaging: Once processed, milk is transferred into various packaging formats, including cartons and bottles. This step not only prepares the product for distribution but also extends its shelf life by protecting it from external contaminants.
Each of these dairy production steps plays a critical role in transforming raw milk into safe, consumable products. By understanding these operations, we can appreciate the complex processes that ensure the dairy products we consume are of the highest quality. These steps are not just about processing milk but also about maintaining the delicate balance between efficiency and safety in milk processing operations.
Essential Equipment in Dairy Manufacturing
In the intricate world of dairy processing, the machinery used is as critical as the processes themselves. The right dairy manufacturing equipment ensures that raw milk is transformed efficiently and safely into a wide array of dairy products. Let’s explore some of the essential equipment found in these plants and understand their roles in the production line.
Equipment | Function | Importance |
Milk Tanks | Store liquid dairy products to maintain freshness. | Crucial for keeping milk fresh before processing, preventing spoilage. |
Separators | Separate cream from milk, producing skimmed milk and cream. | Vital for producing a variety of milk products with differing fat contents. |
Pasteurizers | Heat milk to eliminate harmful bacteria. | Ensures milk safety and extends shelf life, a cornerstone of milk processing machinery. |
Homogenizers | Break down fat molecules for a uniform texture. | Essential for preventing cream separation and enhancing product consistency. |
Cheese Presses | Apply pressure to cheese curds to remove whey. | Key in transforming milk into cheese, affecting texture and quality. |
Butter Churns | Convert cream into butter and buttermilk. | Important for diversifying product offerings, allowing for efficient production of butter. |
Each piece of milk processing machinery plays a pivotal role in the dairy manufacturing process, ensuring that the final products meet quality and safety standards. By understanding the function and importance of these machines, we can appreciate the complexity and precision involved in dairy production. As technology advances, these machines continue to evolve, enhancing efficiency and product quality in plants that process dairy.
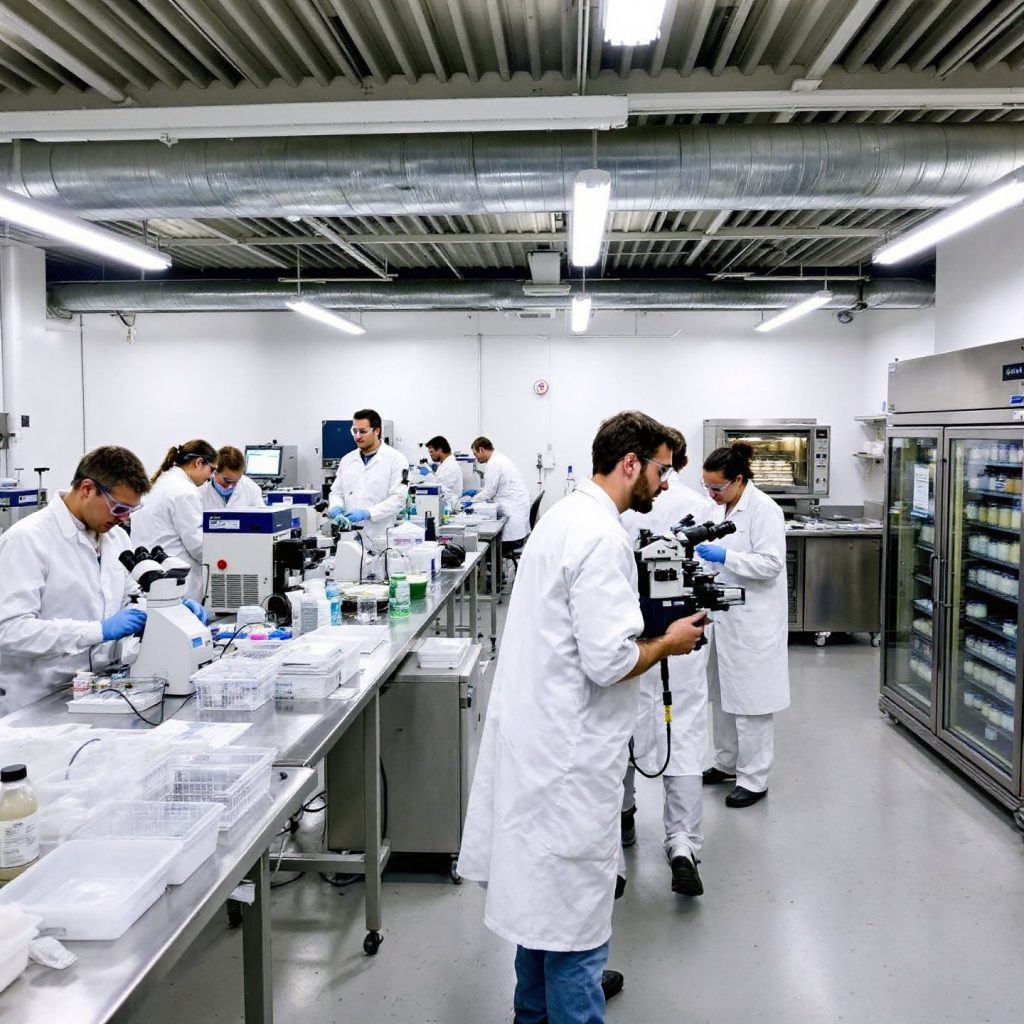
Quality control testing in dairy processing (AI-generated)
Quality Control Measures in Dairy Plants
In the world of dairy processing, ensuring the safety and quality of products is paramount. Quality control measures are meticulously implemented to guarantee that every product meets the highest standards before reaching consumers. But what exactly are these measures, and how do they uphold the integrity of dairy products?
Microbiological Testing
Microbiological testing is a cornerstone of dairy quality control. This involves testing milk and dairy products for harmful bacteria, such as Salmonella and E. coli, which can pose significant health risks. Regular microbiological assessments help identify potential contamination early, allowing for quick corrective actions to be taken. These tests are crucial in ensuring that the final products are safe for consumption.
Chemical Analysis
Another critical aspect of quality control is chemical analysis. This testing protocol verifies the composition of dairy products, ensuring that they meet nutritional labeling standards. For instance, it involves checking the fat, protein, and lactose levels in milk. Chemical analysis helps maintain consistency across batches, ensuring that consumers receive products that match their dietary needs and expectations.
Sensory Evaluation
Sensory evaluation plays a unique role in quality control by assessing the taste, texture, and appearance of dairy products. Trained panels perform these evaluations to ensure that the products not only meet safety standards but also satisfy consumer preferences. This step is vital in maintaining the brand’s reputation and consumer trust.
Regulatory Compliance
Compliance with regulatory standards set by agencies like the FDA and USDA is integral to quality control in dairy processing plants. These standards ensure that products are safe, properly labeled, and free from adulteration. Adhering to these regulations is not just a legal requirement but also a commitment to public health and safety. The FDA’s Milk Safety Cooperative Program, for instance, provides guidance on maintaining these standards through science-based food safety principles (source).
By implementing robust quality control measures, dairy processing plants can effectively safeguard the quality and safety of their products. These protocols, from microbiological testing to regulatory compliance, are essential in maintaining consumer confidence and ensuring that the dairy products we enjoy are both safe and of the highest quality. As we move forward, these measures will continue to evolve, adapting to new challenges and technologies in the ever-changing landscape of dairy production.
Safety and Hygiene Practices in Dairy Processing
When you think about the delicious dairy products lining supermarket shelves, it’s easy to overlook the rigorous safety and hygiene practices that ensure these products are safe to consume. In dairy processing plants, maintaining impeccable hygiene is not just a best practice; it’s a necessity. Let’s explore the essential safety and hygiene practices that keep milk processing operations running smoothly and safely.
Sanitation Procedures
Sanitation is the cornerstone of hygiene in milk processing. One of the most effective methods employed is the Cleaning-in-Place (CIP) system. This automated cleaning process allows for the thorough cleaning of equipment without disassembly, ensuring that every nook and cranny is free from contaminants. CIP systems use a series of rinses and chemical cleansers to sanitize processing lines, tanks, and pipes, effectively eliminating bacteria and other pathogens.
Regular equipment sterilization complements these procedures by providing an additional layer of safety. Sterilization involves using high temperatures or chemical agents to destroy any remaining microorganisms. This step is crucial in preventing cross-contamination and ensuring that each batch of dairy product is as safe as the last.
Importance of Employee Training
Imagine the impact of a single lapse in hygiene practices. It could lead to widespread contamination, posing significant health risks to consumers. This is why employee training is paramount in maintaining hygiene standards. Workers in dairy processing plants are trained in personal hygiene practices, such as proper handwashing techniques and the use of protective clothing like gloves and aprons. Regular health checks are also conducted to ensure that employees are fit to handle dairy products.
Beyond personal hygiene, employees are educated on the importance of adhering to cleaning protocols and the correct use of sanitation equipment. Continuous training programs foster a culture of cleanliness and accountability, ensuring that everyone understands their role in maintaining the highest hygiene standards.
By implementing robust safety and hygiene practices, dairy processing plants can effectively prevent contamination and ensure the production of safe, high-quality dairy products. These measures not only protect public health but also enhance the reputation of dairy brands, building consumer trust and loyalty. As we move forward, the commitment to hygiene in milk processing will remain a critical component of the industry’s success, adapting to new challenges and technologies to meet ever-evolving safety standards.
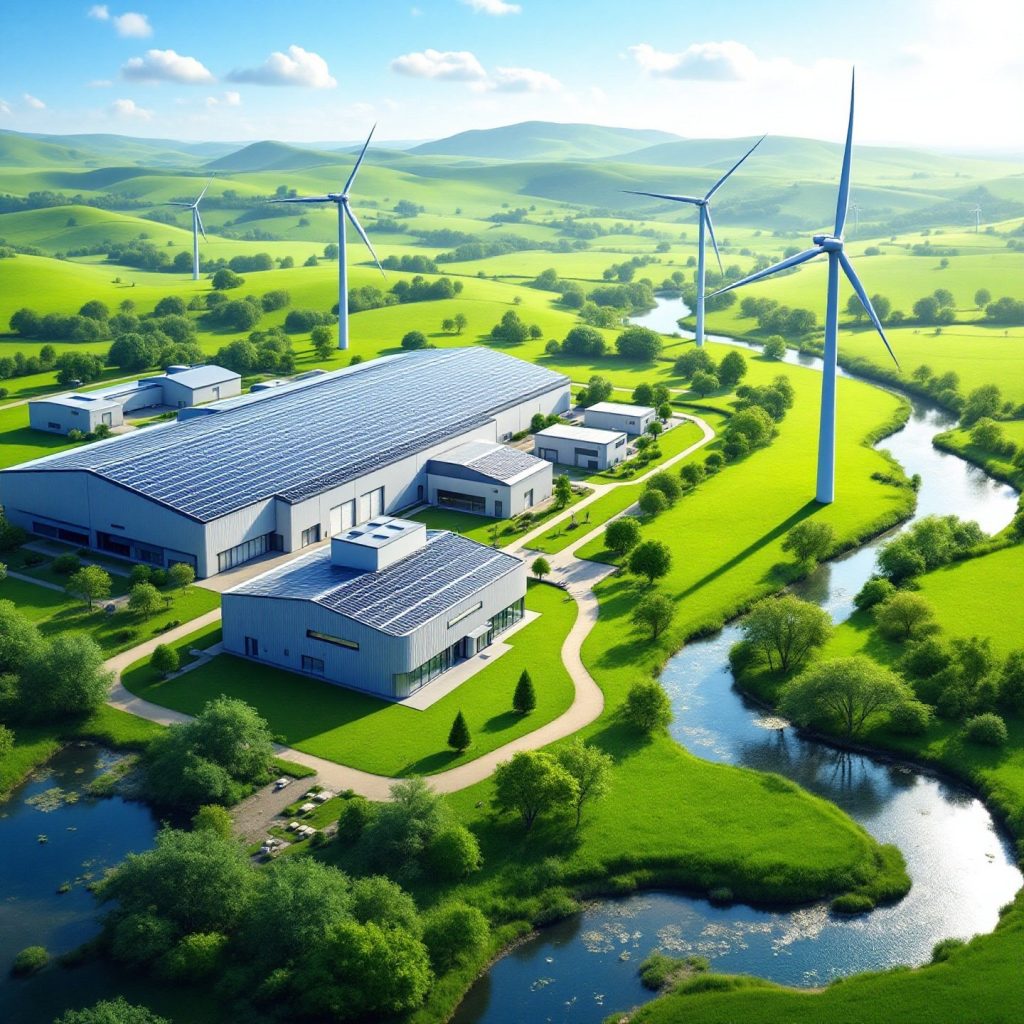
Sustainable practices in dairy processing plants (AI-generated)
Environmental Considerations in Dairy Processing
When you think about dairy processing plants, you might imagine the hustle and bustle of turning raw milk into delicious products. But have you ever considered the environmental impact of these processes? In today’s world, sustainable milk processing is not just a trend; it’s a necessity. Let’s explore how dairy processing plants are addressing environmental concerns through innovative practices and technologies.
Waste Management and Recycling Initiatives
One of the primary environmental challenges in dairy processing is waste management. Plants that process dairy are increasingly adopting recycling initiatives to minimize waste. For instance, dairy farmers and processors are using cow manure as a resource rather than waste. Through anaerobic digesters, manure is converted into renewable energy, reducing reliance on fossil fuels and lowering greenhouse gas emissions. This process not only generates energy but also produces byproducts that can be used as natural fertilizers, enhancing soil quality (source).
Energy Efficiency and Renewable Energy
Energy efficiency is another crucial aspect of sustainable milk processing. Plants are increasingly incorporating energy-saving technologies such as solar panels and energy-efficient machinery. Solar power, for instance, is being harnessed to reduce electricity consumption, particularly during peak sunlight hours. This shift not only cuts down on energy costs but also significantly reduces the carbon footprint of dairy operations (source).
Moreover, the use of renewable energy sources is gaining traction. For example, some dairy farms are utilizing wind and biogas to power their operations, showcasing a commitment to sustainable practices. These initiatives not only contribute to energy independence but also support the broader goal of achieving greenhouse gas neutrality by 2050, as outlined by the U.S. Dairy Net Zero Initiative (source).
Water Conservation and Recycling
Water is an essential resource in dairy processing, and conserving it is a top priority. Plants employ various strategies to recycle water, using it multiple times before it is finally used for irrigation. This approach not only conserves water but also ensures that nutrient-rich water is used to cultivate crops, creating a sustainable cycle that benefits both the environment and the dairy industry (source).
In conclusion, dairy processing plants are making significant strides in reducing their environmental impact through innovative waste management, energy efficiency, and water conservation practices. These efforts are crucial in ensuring that dairy production remains sustainable and environmentally friendly, paving the way for a greener future. As we continue to explore advancements in sustainable milk processing, the commitment to environmental stewardship will remain a guiding principle for the industry.
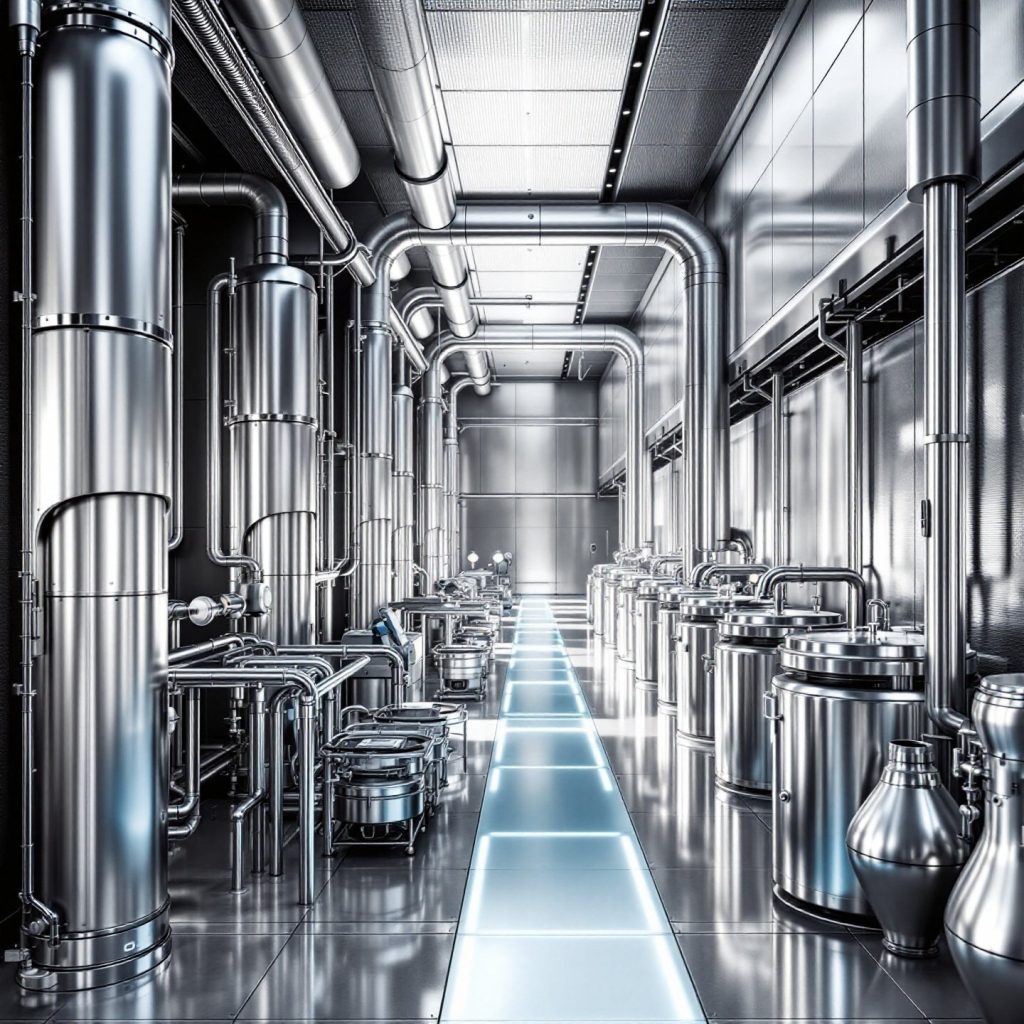
Future trends in dairy processing: automation and sustainability (AI-generated)
Future Trends in Dairy Processing
As we look to the horizon of the dairy industry, it becomes clear that innovation is the key to meeting future challenges and consumer demands. The future of dairy processing is set to be shaped by technological advancements and sustainability efforts, driving the industry towards more efficient and environmentally friendly practices.
Technological Innovations: Automation and Robotics
Imagine a dairy processing plant where robots perform most of the labor-intensive tasks. Sounds futuristic? Not anymore. Automation and robotics are increasingly becoming integral to dairy industry trends. Automated milking systems, for instance, are revolutionizing how milk is collected, reducing the need for human intervention and increasing efficiency. Robotics are also being utilized for packaging and quality control, ensuring precision and reducing human error. These technologies not only enhance productivity but also improve the consistency and quality of dairy products.
Moreover, the integration of Artificial Intelligence (AI) and Machine Learning (ML) is transforming data management in dairy plants. These technologies enable predictive maintenance of machinery, optimizing operations and minimizing downtime. As a result, dairy plants can operate more efficiently, reducing costs and improving output quality.
Sustainability Efforts: Eco-Friendly Packaging and Carbon Footprint Reduction
In response to growing environmental concerns, the dairy industry is making significant strides in sustainability. Eco-friendly packaging is at the forefront of these efforts. Companies are investing in biodegradable and recyclable materials to reduce waste and lessen environmental impact. This shift not only appeals to environmentally conscious consumers but also aligns with global sustainability goals.
Reducing the carbon footprint is another critical focus. Dairy plants are adopting energy-efficient technologies and renewable energy sources to minimize emissions. For instance, solar panels and wind turbines are being used to power operations, significantly cutting down on greenhouse gas emissions. Additionally, innovations in feed composition and livestock management are helping to lower methane emissions, a major contributor to the dairy industry’s carbon footprint.
As the industry continues to evolve, these dairy industry trends highlight the importance of balancing technological advancements with sustainable practices. By embracing automation, robotics, and eco-friendly initiatives, dairy processing plants are not only enhancing their operational efficiency but also contributing to a more sustainable future. These trends are paving the way for a dairy industry that is both innovative and responsible, meeting the demands of modern consumers while safeguarding our planet.
Conclusion: The Critical Role of Dairy Processing Plants and Future Prospects
In the grand tapestry of the dairy industry, processing plants stand as pivotal nodes, ensuring that the milk produced by farmers reaches consumers in a safe, nutritious, and varied form. These facilities are not just about transforming raw milk into consumable products; they are about upholding the highest standards of quality and safety, which are essential for public health and economic sustainability.
Dairy processing plants are at the heart of the industry, facilitating the conversion of raw milk into a myriad of products that cater to diverse consumer needs. From traditional staples like cheese and butter to innovative offerings like lactose-free and fortified milk, these plants are crucial in maintaining the supply chain’s integrity. They employ advanced technologies and rigorous quality control measures to ensure that every product meets stringent safety standards, thereby protecting consumer health.
As we look to the future, innovation within these plants will be paramount. The integration of automation and robotics is set to redefine efficiency and precision in processing operations. Similarly, sustainability efforts, such as eco-friendly packaging and reduced carbon footprints, will continue to shape the industry’s trajectory, aligning with global environmental goals.
Beyond dairy, there’s growing interest in plant-based alternatives, which offer numerous plant milk benefits such as lower environmental impact and health advantages. Plant-based milks, like almond and soy, are not only heart-healthy but also contribute to reducing greenhouse gas emissions. For those interested in exploring these alternatives, investing in a plant milk maker can be a rewarding choice, providing convenience and control over ingredients.
In conclusion, while dairy processing plants remain indispensable to the industry, the rise of plant-based options reflects a broader shift towards sustainability and health consciousness. Whether you’re a dairy enthusiast or exploring plant-based alternatives, understanding these dynamics can enrich your choices. For those keen on delving deeper into plant-based milk production, consider exploring the top plant milk makers of 2025 here.
Frequently Asked Questions
1. What is a milk processing plant?
A milk processing plant is a facility where raw milk is processed into various dairy products like cheese, yogurt, and butter. These plants ensure safety and quality through processes like pasteurization and homogenization, playing a crucial role in the dairy industry.
2. How do dairy processing plants ensure product safety?
Dairy processing plants implement quality control measures such as microbiological testing, chemical analysis, and sensory evaluation. These steps, along with regulatory compliance, ensure that dairy products are safe for consumption.
3. What are some key operations in dairy processing?
Key operations include reception and testing of raw milk, separation, standardization, pasteurization, homogenization, and packaging. Each step is crucial for transforming raw milk into safe, high-quality dairy products.
4. How do dairy plants address environmental concerns?
Dairy plants adopt sustainable practices like waste management, recycling, and energy efficiency. They use renewable energy sources and water conservation techniques to minimize environmental impact.
5. What future trends are shaping the dairy processing industry?
The industry is advancing with automation, robotics, and sustainability efforts like eco-friendly packaging. These trends aim to enhance efficiency and reduce the dairy industry’s carbon footprint.